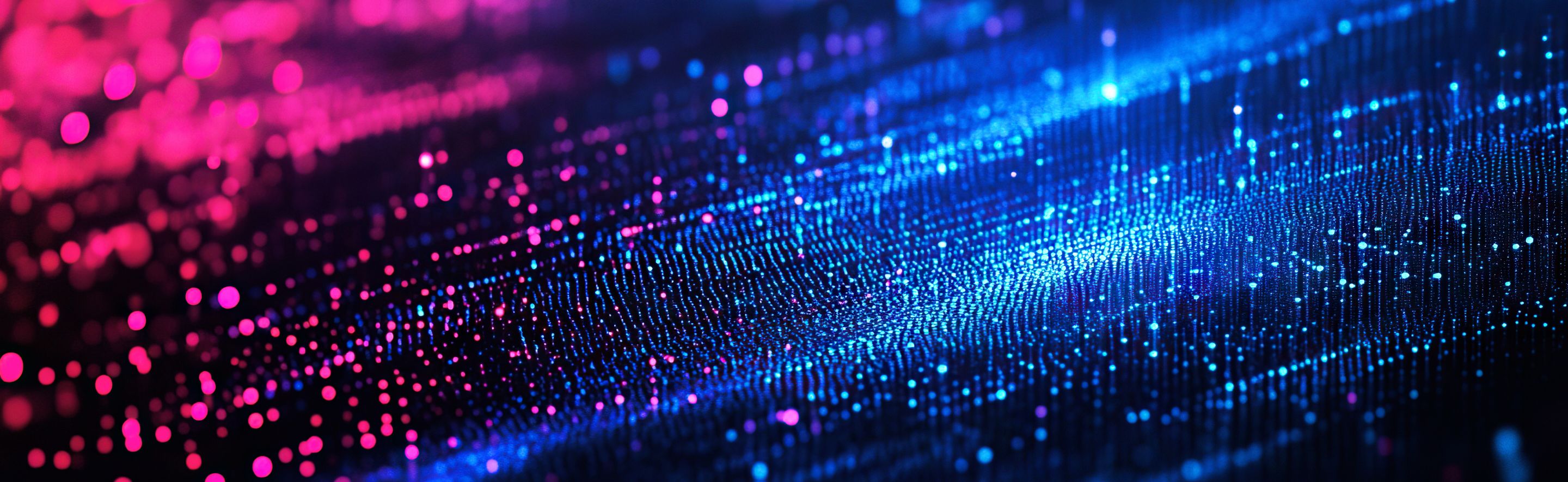
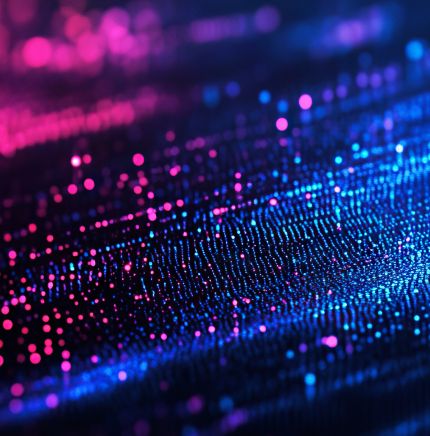
News
Engineering the Smart Factory: Tata Elxsi’s Blueprint for Intelligent, Sustainable Manufacturing
Date: May 20 2025
Publication: Pi-india.in
In a rapidly evolving industrial landscape, where smart technologies are redefining every layer of manufacturing, Tata Elxsi is at the forefront of engineering transformation. In an exclusive conversation with Efficient Manufacturing, Kaushik Pal, Head of Systems Integration Services at Tata Elxsi, shares how the company is driving innovation through its Centres of Excellence in AI, IoT, and Extended Reality. From predictive safety systems and immersive design validation to scalable test automation and green energy solutions, Tata Elxsi is blending cognitive intelligence with real-world engineering to build the factories of tomorrow: intelligent, interconnected, and sustainable.
As India accelerates its adoption of Industry 4.0, how is Tata Elxsi leveraging its COEs in AI, IoT, and Extended Reality to redefine the future of smart manufacturing?
Our AI, IoT, and Extended Reality Centres of Excellence (COEs) at Tata Elxsi are created specifically to propel next-generation smart manufacturing. These COEs are innovation hubs where concepts are put into practice, not just acting only as think tanks. Through the integration of immersive technology, predictive analytics, and intelligent automation, we are assisting factories into becoming interconnected ecosystems. Our solutions enable cost-effective digital transformation and are customised to meet the needs of Indian industry, especially MSMEs. On the shop floor, we’re facilitating quicker, more intelligent decision-making with cross-platform integration and real-time data visibility.
Can you elaborate on how AI-focused safety monitoring systems are transforming workplace safety in high-risk industrial environments?
Workplace safety cannot be compromised, particularly in dangerous industrial areas. For this reason, our AI-driven safety monitoring systems are made to proactively detect threats before they become more serious. We make real-time tracking of human-machine interaction possible using computer vision, wearables, and predictive alert systems. More excitingly, we’re using Extended Reality (XR) to securely simulate risky events for training, giving staff members the assurance, they need to manage critical circumstances. The goal is to create a culture of safety by design, which goes beyond compliance.
Digital twins are gaining traction in industrial applications. How is Tata Elxsi deploying AI-driven digital twin technology to simulate real-world scenarios and optimise product lifecycle management?
One of the core practices of our Industry 4.0 strategy are digital twins. In a virtual environment, we assist clients in simulating and tracking each stage of the product lifecycle. These digital twins, which are powered by AI, provide profound insights into performance, predictive maintenance, and failure modes in addition to mirroring processes and learning and evolving. For example, our digital twin solutions are used to model assembly line behaviours and environmental effects in the automobile industry, allowing for quicker iterations, less downtime, and optimised resource planning & allocation.
Immersive visualisation is revolutionising design validation. Could you share examples of how it helps engineers refine product designs before physical prototyping?
The way engineers approach design is changing as a result of immersive visualisation. Before a single bolt is tightened, picture being able to enter a fully interactive 3D model of your product, see anomalies, and make adjustments in real time collaboratively. That is the power of our XR solutions and services. Our immersive technology saved weeks of redesign and rework by allowing our client’s teams to virtually tour a factory layout, identify ergonomic problems, and optimise workflow in one of our engagements with a top manufacturing client. Time-to-market is accelerated, and material waste is greatly decreased.
With sustainability becoming a core priority, how are your enhanced battery and motor control technologies helping clients reduce energy consumption and meet global green goals?
Sustainability isn’t just a checkbox for us—it’s embedded in our engineering DNA. Our advanced battery and motor control systems are designed to optimise energy efficiency across electric mobility and industrial automation. By enabling precise torque and speed control, we’re reducing energy leakage and enhancing battery life. Clients using our solutions have reported up to 15% improvements in energy efficiency. These innovations are helping manufacturers align with global green mandates while achieving cost efficiencies—a win-win for business and the planet.
Your software testing automation framework claims to reduce defined testing time by 40% and improve operational efficiency by 30%. What are the underlying technologies and how scalable is this solution across different manufacturing sectors?
Our AI-driven software testing automation framework combines several cutting-edge technologies to streamline testing cycles, reduce manual effort, and significantly boost reliability. At its core, it leverages Generative AI powered by large language models (LLMs) to automatically generate test cases, scripts, and even edge-case scenarios directly from requirement documents or user stories. This not only speeds up the test creation process but also allows the framework to adapt and evolve with ongoing product changes through continuous learning.
To handle repetitive tasks, the framework integrates Robotic Process Automation (RPA), making it possible to automate everything from test execution and data entry to regression and UI validations, all with minimal human involvement. Enhancing this further, AI and machine learning-based predictive analytics play a key role in identifying potential failure points and intelligently prioritising test cases using historical defect data and system complexity. This means teams can focus their efforts on areas that matter most, ensuring smart and efficient test coverage.
The framework is also built on a low-code/no-code foundation, empowering QA teams and even domain experts to design and deploy test flows without deep scripting knowledge, improving agility and cross-functional collaboration. Finally, with a cloud-native and containerised architecture using tools like Kubernetes and Docker, the solution supports large-scale, parallel test execution and fits seamlessly into modern CI/CD environments such as Jenkins, GitLab, and Azure DevOps. Together, these technologies enable a reduction in execution time of up to 40% while driving operational efficiency by as much as 30%.
Our automation solution is highly scalable and customizable. It has already demonstrated success in diverse sectors such as automotive, electronics manufacturing, and industrial robotics, thanks to its plug-and-play design and compatibility with major manufacturing systems. The modular architecture allows for seamless integration with existing MES and PLM systems, ensuring faster deployment and ROI realisation.
By merging cognitive intelligence with physical automation, Tata Elxsi’s framework is enabling future-ready factories to become more agile, data-driven, and operationally efficient.