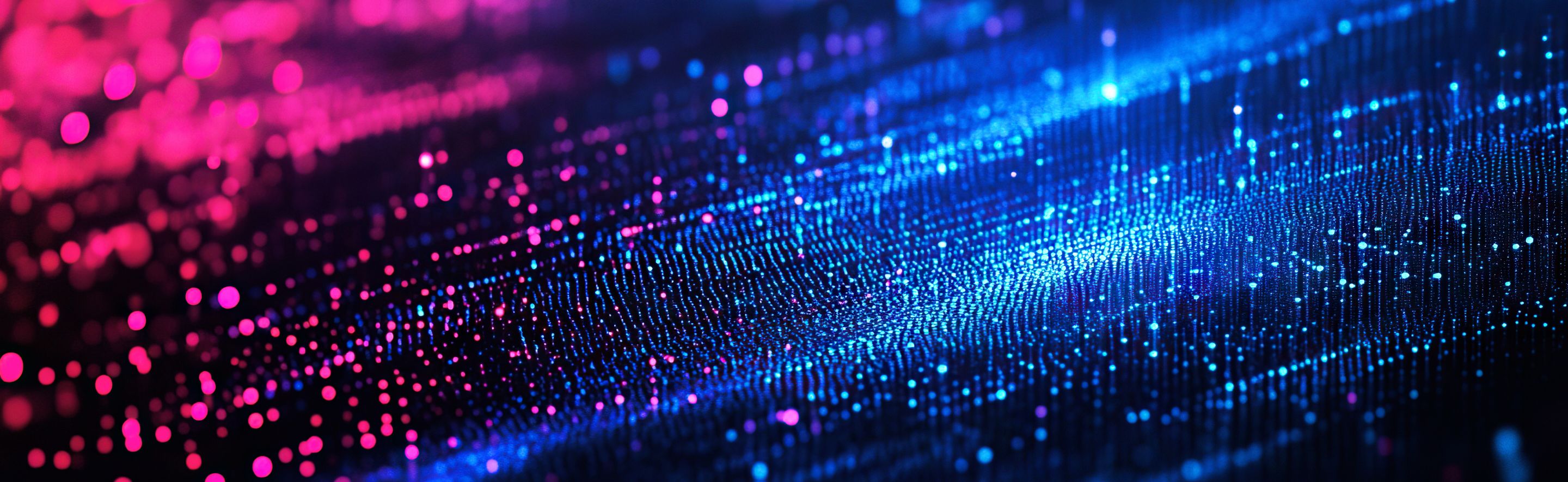
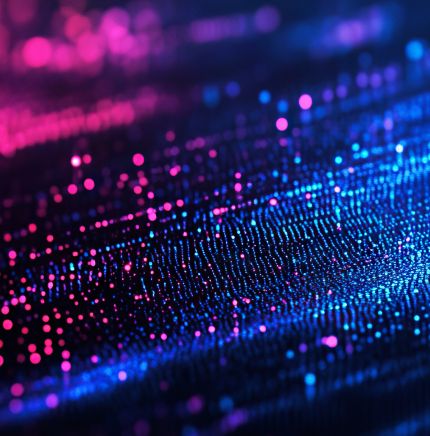
News
Tata Elxsi pushes immersive tech and SaaS models for safety and training for MSMEs
Date: Apr 16 2025
Pbulication: www.oemupdate.com
In this exclusive interview, Kaushik Pal, Head of Systems Integration Services at Tata Elxsi, shares how they use the learner’s approach, where they deploy their technology internally and in Tata Group companies to bring out the best possible innovations for the manufacturing industry.
How is Tata Elxsi contributing to the growth and advancement of the manufacturing industry?
We have established numerous global partnerships with manufacturing companies to help them adopt the latest technologies. Transitioning from legacy manufacturers to new-generation ones involves navigating a variety of complexities. For instance, many factories have a mix of legacy and new machines that need to be interconnected, creating a complex environment within the plant.
Our team assists manufacturers in sensitising their machines. We work at the foundational level, also known as the device layer, where machines are equipped with sensors to communicate via an IP address. The second layer involves our Tether platform and Tether factory platform. These platforms aggregate incoming data, intelligently analyse what is happening within the plant, and visualise reports. As part of the Tata Group, we also benefit from our exposure to various verticals within the organisation, which enables us to develop numerous use cases based on the data collected.
Once data is gathered, the challenge lies in determining how to leverage it effectively and generate value. This is where we engage in building use cases, project oversight, and various initiatives to help manufacturers derive value from their data, ultimately supporting their operational needs.
In addition to assisting existing manufacturers, we also work with new plants established in our country, which are considered greenfield setups. In these cases, we emphasise simplicity and provide consultations on how to design their plants efficiently. We recommend the right types of machinery, integration platforms, and strategies for connecting this data to their enterprise systems.
How do you address cybersecurity challenges in modern manufacturing environments, especially with the increasing number of connected devices and potential external threats?
This issue extends beyond the factory; it affects all devices in use. Every device is susceptible to threats. We have developed an advanced cybersecurity practice and operate a command and control security operation centre where we monitor activities 24/7. This is facilitated by various tools, a team of cybersecurity experts, and partnerships with different cybersecurity providers. We can offer continuous monitoring of activities within the manufacturing plant.
For example, if someone brings their device into the plant, we can identify potential threats that may arise. Additionally, we are examining various layers of security. This includes securing the network and application layer and implementing an overall cybersecurity framework. By fortifying different layers of security, we can create a comprehensive cybersecurity strategy.
Connected vehicles have significantly advanced in recent years. Today, having access to your car via a mobile app is almost essential when buying a new vehicle. While this may seem simple for users, a complex technology infrastructure supports it.
Telematics technology plays a crucial role, as it collects real-time data from the vehicle. This data must be effectively transmitted to various systems that intelligently analyse millions of data points from OEMs and users. As technology becomes simpler and bandwidth increases, vehicles can process data more efficiently on the edge, optimising what gets collected and transmitted.
This data provides valuable insights into vehicle performance, allowing for better future design for OEMs. Users benefit from features like fuel consumption tracking and theft prevention, with the number of available features growing from today’s 50 or 60 to potentially 500 in the future.
On the manufacturing side, the landscape is evolving. Where customisation options were once limited, buyers can now customise vehicles extensively online. Modern manufacturing plants must be agile to manage various customisations and model platforms in a single production line, allowing unique vehicles to be produced around the clock.
This connected manufacturing ecosystem enhances visibility for a more flexible production environment. I envision future plants where everything except the roof could be customisable.
The connected ecosystem also helps gather insights into user behaviour and increases connections with insurance providers for better package deals. These improvements will enhance vehicle serviceability and maintenance. Currently, at Tata Elxsi, we handle about 600 TB of live data from connected vehicles, providing valuable feedback to OEMs on performance.
Tata Elxsi has been at the forefront of digital transformation. What are some of the most exciting innovations currently being developed in your Business Unit?
We are automating our processes as part of our digital transformation journey. This transformation focuses on three layers: the enterprise layer, which encompasses our IT systems and infrastructure, ensuring that they support this evolution and are efficient in monitoring network and security operations 24/7.
Our 24/7 IT infrastructure support can be automated to reduce operational shifts from three to two. One shift will become a “dark shift,” meaning it will require no electricity or human intervention due to high levels of automation.
A multitude of technologies is emerging for real-time monitoring and triaging. For instance, immediate action is required in the event of a cyber attack, which is challenging with human interventions. This necessity has driven advancements in intelligent system interactions.
The second layer pertains to IoT, which includes connected vehicles, factories, and assets. We heavily invest in understanding how to monitor these assets in real-time. Our Tether platform, currently deployed in Tata Motors vehicles, operates over 1.5 million vehicles on the road. We must maintain complete visibility of how data is collected from these vehicles. We aim to analyse this data to provide feedback to OEMs and end-users in case of any anomalies.
For example, we are trying to predict when a car needs maintenance before a breakdown occurs. We are analysing whether the vehicle in an unsecured environment can trigger before an incident happens. In cases of accidents with airbag deployment, can we contact emergency services automatically before you call them?
The third layer focuses on the user experience. Significant advancements are being made in digital transformation, such as enhanced human-machine interfaces, with substantial investments from Tata Elxsi. Previously known as a design engineering company, we have made design the core of our service philosophy. Every interaction you have with the machines we develop must be both highly engaging and valuable.
Additionally, we help automotive and heavy engineering manufacturers collaborate globally using virtual and mixed-reality technologies, streamlining their go-to-market solutions. We create digital twins to validate product designs before production, ensuring they meet performance expectations. With over 40 Centers of Excellence and partnerships with top manufacturers in India, we are positioned as a market leader, leveraging India’s resources to enhance R&D cycles for major OEMs like Mercedes-Benz. Our advanced capabilities in virtual and mixed reality further strengthen our competitive edge.
Tata Elxsi collaborates with various Tata Group companies. How do these partnerships contribute to the company’s innovation and business growth?
Tata Elxsi has traditionally been involved in the established sectors of the Tata Group, such as retail, steel, motors, and automotive. We are exploring new-age businesses like semiconductors, batteries, electronic components, and mobile phone manufacturing.
We are actively working to become a manufacturing partner and R&D partner, focusing on designing interventions and contributing from the initial stages of factory development. Our emphasis is on understanding the landscape and ensuring safety throughout the process.
We aim to develop more interactive approaches in terms of safety strategies for large plants. We have utilised data in different capacities and will continue to support startup companies.
When we present our solutions externally, they are often grounded in practical experience rather than theoretical concepts that we gain from working with TATA Group Companies. This hands-on approach stems from our commitment to thoroughly testing and refining solutions within our group and the company.
What impact do emerging technologies like AR and VR spatial computing have on industrial training, worker safety and manufacturing processes?
There is a strong push from the government to prioritise worker safety within the manufacturing industry. We have been collaborating with some of the largest manufacturers in India to create their safety training strategies and infrastructure, both physical and digital components.
Augmented Reality (AR), Virtual Reality (VR), and Mixed Reality (MR) play a significant role in this process. We have developed environments where safety workers can first experience the physical aspects of safety. They then transition into a digital environment, utilising AR and VR technologies to visualise what a factory setting looks like.
These workers also engage with MR experiences. For instance, when working near a high-voltage tower, safety personnel must adhere to standard operating procedures (SOPs) because it’s a high-voltage environment. Through haptic interventions, we can simulate experiences for safety workers, illustrating the potential repercussions of not following these procedures.
Workers can repeatedly experience the sensation of receiving an electric shock or the fear of falling from a high tower. This immersion creates a deeper understanding and adherence to SOPs over time. The intersection of safety, manufacturing, and immersive technologies like VR and MR is gaining traction.
Many companies are adopting digital or immersive training methods because they provide more effective learning. Traditional classroom-based training has limited retention rates, whereas immersive experiences engage workers more directly. This is particularly important considering that many workers, often with limited educational backgrounds, may struggle to retain information from lengthy training sessions.
Companies can expedite complex training by condensing 6-8 hours of lecture into a one-hour session, yielding better results than traditional methods.
In a large manufacturing plant with 5,000 to 20,000 employees, a significant portion may be illiterate, with around 40 to 50% attrition occurring annually. When combined with the challenges of a hazardous environment and an unskilled labour force, this situation presents a substantial problem. This is why many organisations are investing heavily in developing innovative training solutions.
How are you adapting your safety and automation solutions to meet the specific needs and constraints of MSMEs?
The business models that have been successful for larger manufacturers do not necessarily apply to MSMEs. Therefore, we are working on developing more packaged solutions. For instance, when it comes to content manufacturing, we can offer ready-made solutions, such as a sensor integrated with a platform, operational expenditure (OPEX) models, or subscription services.
We are exploring Software as a Service (SaaS) models, which convert capital expenditure (CAPEX) into OPEX, ultimately enhancing safety for these manufacturers. Our goal is to create miniature versions of safety modules that can easily plug into existing factories. This approach will reduce complexity and budget requirements while still meeting safety needs.
We are refining our solutions and making them more user-friendly for adoption. Additionally, we provide MSMEs with tours of more mature facilities to help raise awareness.