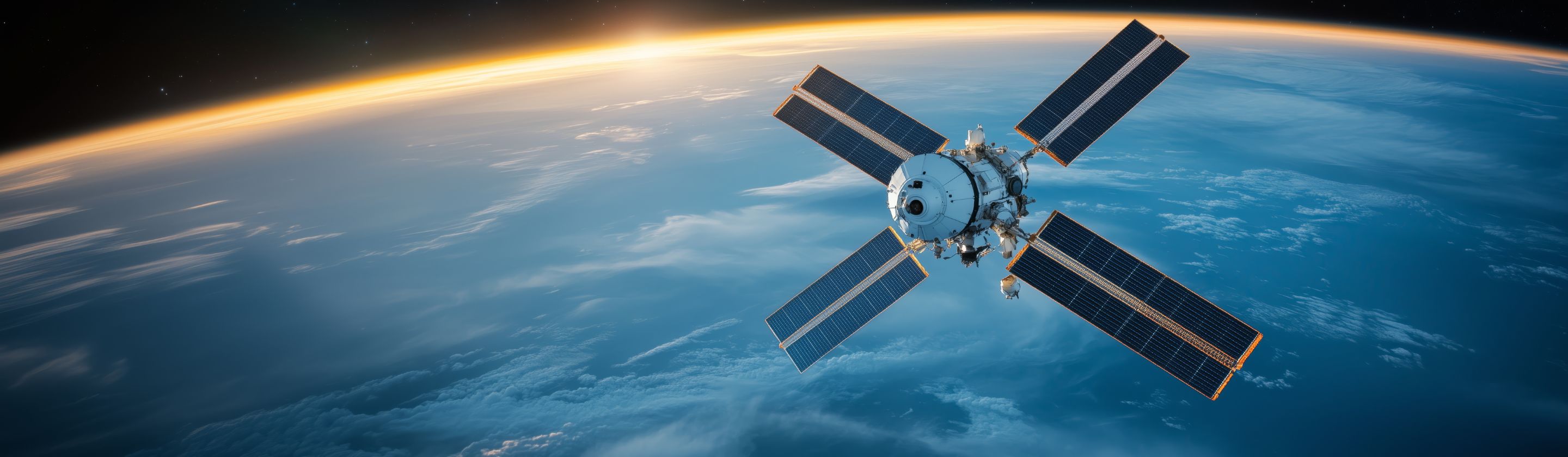
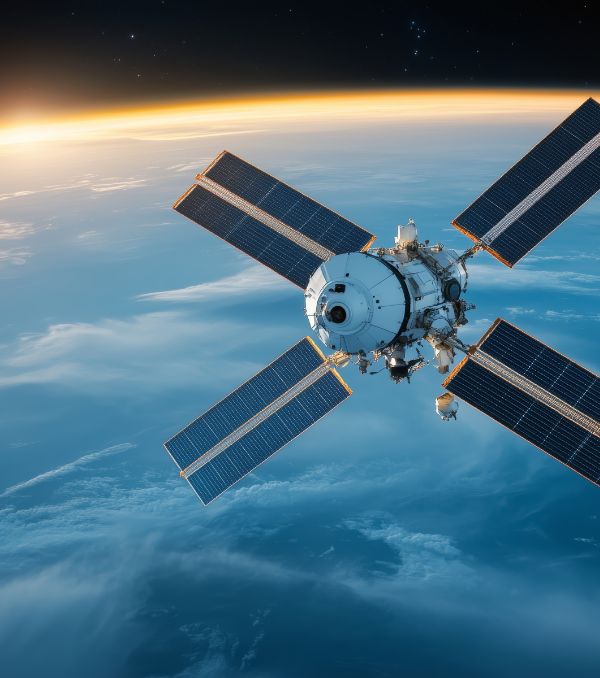
CMRM for ISRO's Gaganyaan Space Mission
Design, Development and Fabrication of Crew Module Recovery Model (CMRM) for ISRO's Gaganyaan Space Mission.
Read Case StudyDesigning for the Skies Ahead
In an era where safety, reliability, and efficiency define success, aerostructure design and engineering stands as the backbone of next-generation aircraft development. At Tata Elxsi, we fuse digital engineering with domain expertise to deliver robust aerostructure solutions that accelerate time-to-market, optimize costs, and enhance operational excellence for global aerospace leaders.
By leveraging lightweight materials, advanced simulation, and data-driven insights, we address complex aerospace challenges with agility. Each lifecycle phase meets stringent standards, ensuring reliability, sustainability, and a competitive edge. We also integrate manufacturing best practices to reduce waste and deliver lighter, more reliable aircraft structures.
Business Challenge
The aerospace industry is under pressure to deliver first-time-right designs at accelerated timelines, while meeting stringent safety and performance standards. As aircraft electrification and sustainability goals rise, engineering teams must balance complex design requirements, lightweight materials, and advanced simulations with manufacturability and tooling constraints. This calls for a shift toward AI-led and knowledge-based engineering, enabling faster, smarter, and more reliable product development.
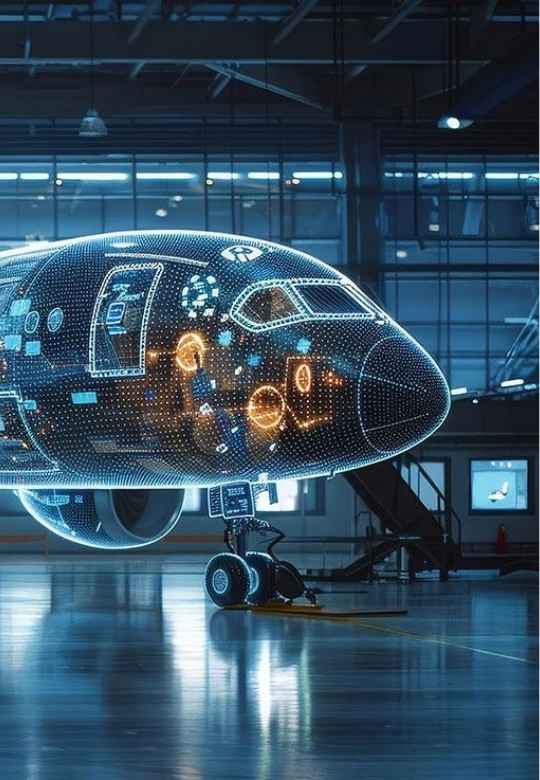
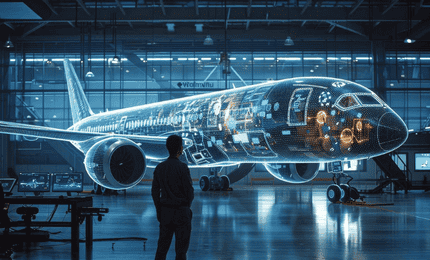
Here’s How We Help
Turnkey Aerostructure Programs
- We deliver turnkey programs in aerospace structural engineering, covering concept design, calculations, materials selection, simulations, mockup, and tooling for robust performance.
- This holistic approach addresses aerodynamics, VA/VE, and critical parameters, ensuring cost-effective aerostructures that exceed industry benchmarks.
Emphasis on Lightweighting & Sustainability
- Our materials and simulation teams optimize metallics, composites, and additive manufacturing to reduce weight while maintaining structural integrity.
- We balance cost, ease of sourcing, and emissions goals to create environmentally conscious aerostructures.
Advanced Simulation & Digital Tools
- Digital twins enable real-time performance monitoring and faster iterations, accelerating product development and design refinement.
- Combining KBE, CAD & CAE automation, and multi-physics simulations (aeroelasticity, fatigue, fracture), we shorten development cycles and ensure optimal load conditions.
Solution Framework
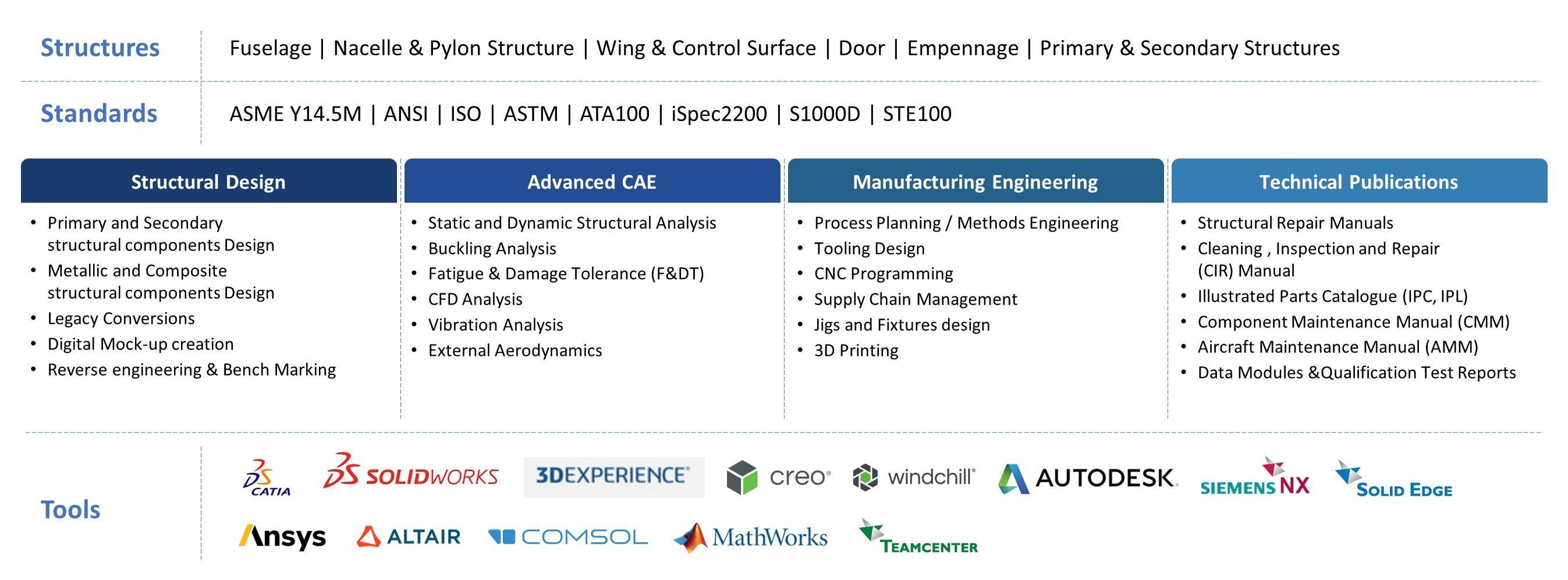
At Tata Elxsi, we provide end-to-end aerospace engineering services that cover every stage of the product lifecycle. Our expertise spans structural design, advanced CAE, and manufacturing engineering. We specialize in metallic and composite structures, static and damage tolerance, and Digital Mock-Up (DMU) development. Our solutions ensure high-quality, reliable, and sustainable aerostructures that meet the industry's evolving demands for speed, efficiency, and performance.
Advanced Simulation & Analysis
Through state-of-the-art simulation, computational fluid dynamics (CFD), and finite element analysis (FEA), we predict structural behavior under extreme conditions. This approach identifies potential risks early, ensuring optimized design and reduced rework. Our holistic analysis covers stress, fatigue, and aerodynamic performance, yielding safer, more reliable, and cost-effective aircraft structures. Data-driven modeling further refines design iterations swiftly.
Lightweight Material Expertise
Composites and lightweight alloys are crucial for fuel efficiency and aircraft performance. Our experts evaluate material properties, explore cutting-edge bonding techniques, and integrate eco-friendly solutions wherever feasible. By focusing on strength-to-weight ratios and recyclable materials, we help our clients reduce carbon emissions and lifecycle costs without compromising on structural integrity.
End-to-End Project Management
In aerospace, timely delivery and rigorous quality assurance are non-negotiable. Our end-to-end project management covers design planning, resource allocation, risk assessment, and regulatory compliance at every milestone. By coordinating global supply chains, scheduling prototypes, and monitoring performance metrics, we ensure seamless program execution that meets critical launch windows and budget targets.
Why Tata Elxsi?
- Proven expertise in aerospace engineering, consistently delivering optimized, regulatory-compliant solutions for complex, mission-critical programs worldwide.
- Highly skilled engineering teams with cross-functional backgrounds, ensuring end-to-end coverage from concept to manufacturing integration.
- Robust digital engineering capabilities that accelerate time-to-market and enhance product performance through valuable data-driven insights.
- Proven track record of on-time delivery, leveraging global partnerships for globally streamlined supply chain management.
- Holistic approach to sustainability, embedding eco-friendly materials and practices without compromising performance or regulatory standards.
Testimonial
Testimonial
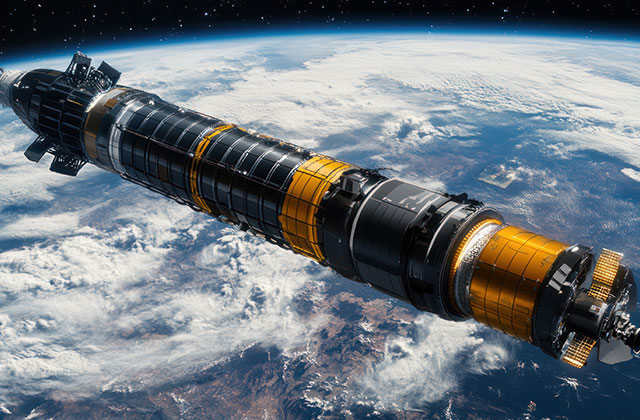
Indian Space Research Organisation (ISRO)
“Tata Elxsi has carried out the design and delivered hardware meeting a highly challenging delivery schedule of 6 months, demonstrating excellent program management skills. This has enabled timely commissioning recovery training exercise to meet Gaganyaan mission requirements. ISRO would definitely like to partner in the future for different projects.”
Dr. Umamaheshwaran, Director-HSFC, ISRO
Information Hub
-
What trends are shaping the future of aerostructure design and engineering?
Lightweight composites, intelligent automation, and Additive Manufacturing (AM) are redefining aerostructure design. As fuel efficiency and lower emissions become top priorities, materials research is moving toward sustainable and recyclable compounds. Moreover, digital twins allow real-time monitoring of structure health, minimizing maintenance downtimes. The rapid adoption of Industry 4.0 tools—like augmented reality and machine learning—further optimizes production and quality control. These emerging technologies, combined with ever-tightening safety regulations, underscore the importance of a holistic, future-ready approach for OEMs and suppliers to stay competitive and meet evolving global aerospace demands.
-
How does Tata Elxsi ensure compliance with aerospace standards and regulations?
Compliance starts at the design phase, where our teams integrate aerospace regulations like FAA and EASA guidelines into engineering workflows. We follow a stage-gate process that includes risk assessments, verification, and validation at every step. Our quality management system is AS9100 certified, reflecting adherence to stringent standards. Additionally, we collaborate with certification bodies to keep pace with industry updates, ensuring each aerostructure design meets or exceeds safety and performance thresholds. By combining robust documentation with proactive engineering reviews, we deliver solutions aligned with global aerospace benchmarks.
-
What are the benefits of using advanced simulation tools in aerostructure engineering?
Advanced simulation tools like CFD and FEA drastically reduce physical prototyping and testing costs. They enable engineers to predict stress, vibration, and thermal behaviors under various flight conditions, identifying potential failure points early. By simulating material interactions and load distributions, teams refine designs for optimal weight and structural performance. This virtual validation approach accelerates the development timeline, diminishes rework, and enhances safety. Moreover, data-driven modeling improves decision-making, allowing precise trade-off analysis between cost, efficiency, and longevity, ultimately ensuring a competitive and reliable final product.
-
How do aerostructure engineering solutions impact overall aircraft performance?
Effective aerostructure design ensures reduced aircraft weight, leading to enhanced fuel efficiency and lower operational costs. Proper structural optimization also improves aerodynamic flow, minimizing drag and maximizing lift. By integrating advanced materials and precision engineering, the aircraft gains better strength while maintaining lightness, critical for safety and durability. Additionally, well-designed aerostructures simplify maintenance, allowing quicker turnaround times and extended service intervals. Overall, a robust aerostructure elevates flight performance, reliability, and passenger experience, ensuring a competitive edge for airlines and OEMs in a rapidly evolving aerospace industry.
-
What role does digital transformation play in modern aerostructure engineering?
Digital transformation revolutionizes aerostructure engineering by integrating cloud-based collaboration, AI-driven analytics, and IoT-enabled smart factories. This connected ecosystem provides real-time data on manufacturing, maintenance, and performance parameters, helping engineers make informed, iterative improvements. Virtual reality and augmented reality solutions streamline training and design reviews, while predictive analytics minimize downtime through proactive maintenance scheduling. With digital technologies, aerospace firms can shorten development cycles, control costs, and maintain quality across global supply chains. By seamlessly linking design, production, and operations, digital transformation underpins agile, efficient, and innovative aerostructure solutions.