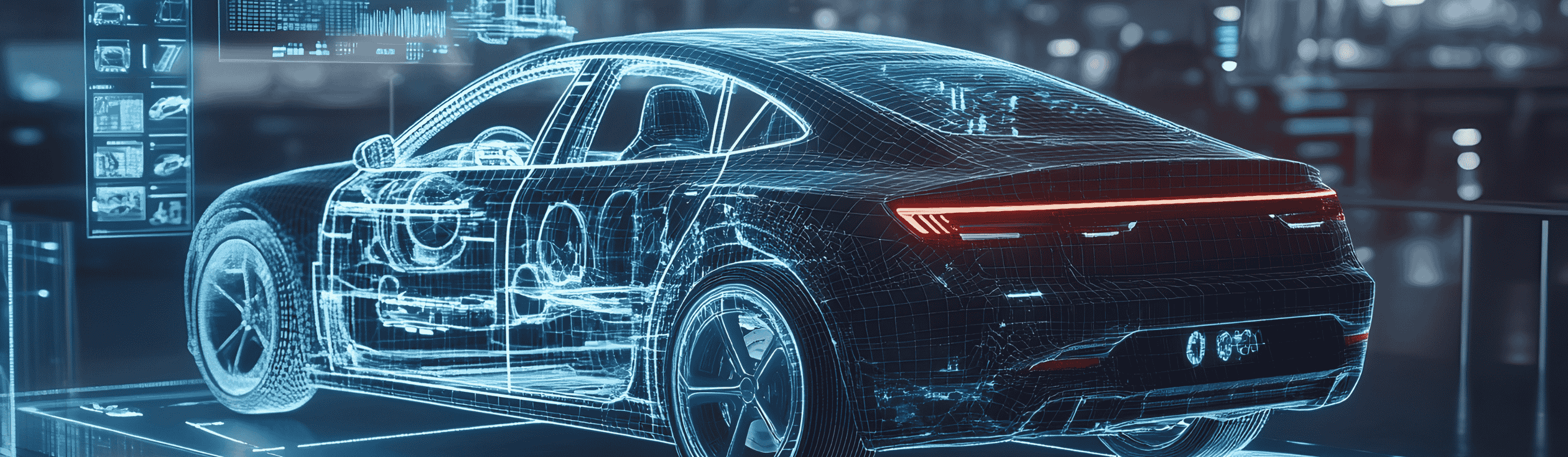
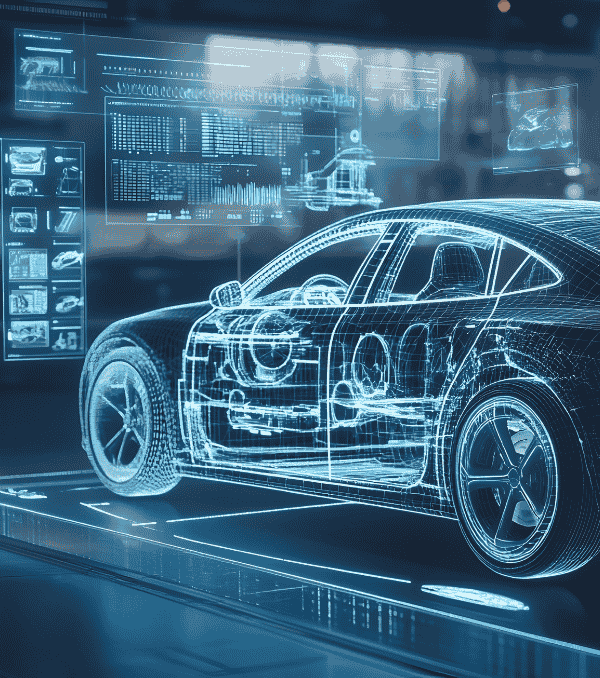
Accelerating Unit Testing using Generative AI
The significant impact of GenAI in accelerating unit testing processes in software development.
Read ArticleTrending
Rapid electrification in the automotive sector is reshaping consumer behavior, driven by stringent regulatory pressures to reduce carbon emissions and advances in battery charging and electric powertrain technologies. As electric vehicles (EVs) evolve, a surge in V&V (Verification & Validation) cycles is required to ensure that every component meets strict functional safety standards. This rise in software-defined architecture is accompanied by an exponential increase in data flowing through vehicle E/E systems.
Simultaneously, the demand for modular, cost-effective, and scalable solutions has never been more critical. Automotive engineers must integrate flexible HILS (Hardware-in-the-Loop Simulation) setups and real-time validation to build a truly safe and reliable electric vehicle ecosystem.
Business Challenge
A significant spike in software requirements coupled with functional safety compliance and ECU consolidation brings considerable challenges for software architecture design and integration. Validation at various integration points, Design, and development of a flexible and cost-effective EV test system, Replicating Test Scenarios in the Real World are some of the challenges faced in EV Testing. Our EV testing services offers customers software & system qualification and integration testing services and also a quick, flexible and ready-made test system. This can be utilized at the component level as well as at the system level, based on the requirements. As most of the components are readily available and designed with high modularity, the HILS infrastructure can be set up faster.
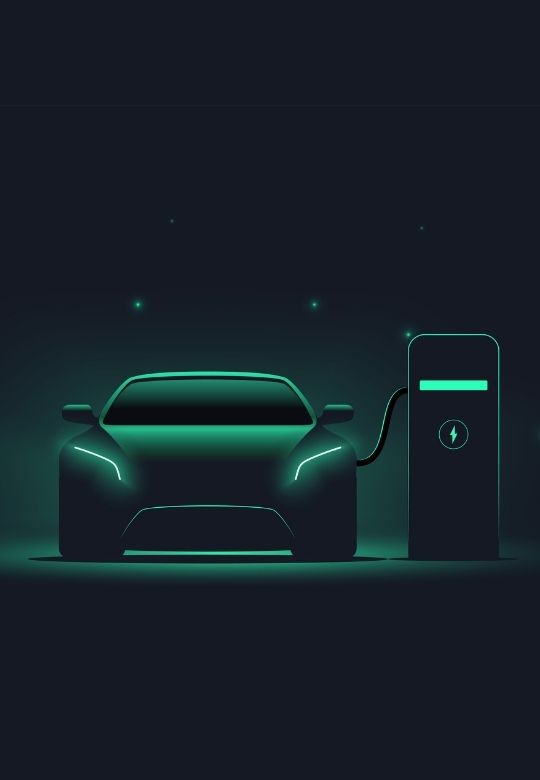
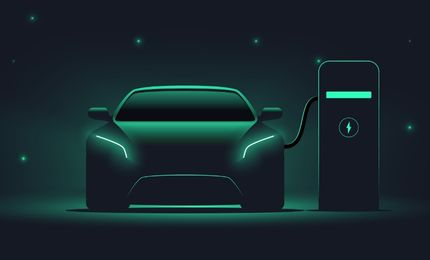
Here’s How We Help
Integrated Software & System Qualification
- Perform end-to-end software validation across ECUs to meet functional safety compliance.
- Ensure seamless integration testing to handle exponential increases in software requirements.
Rapid Test Bench Setup & Modularity
- Deploy a ready-made test system that scales from component-level checks to system-level evaluations.
- Utilize NI test bench with Dyno load control for replicating complex real-world scenarios.
Holistic Validation Services
- Provide whole vehicle validation through a reusable framework—enabling faster HILS infrastructure deployment.
- Incorporate solutions like VDrive to simulate drive scenarios, ensuring rigorous real-time EV testing.
Solution Framework
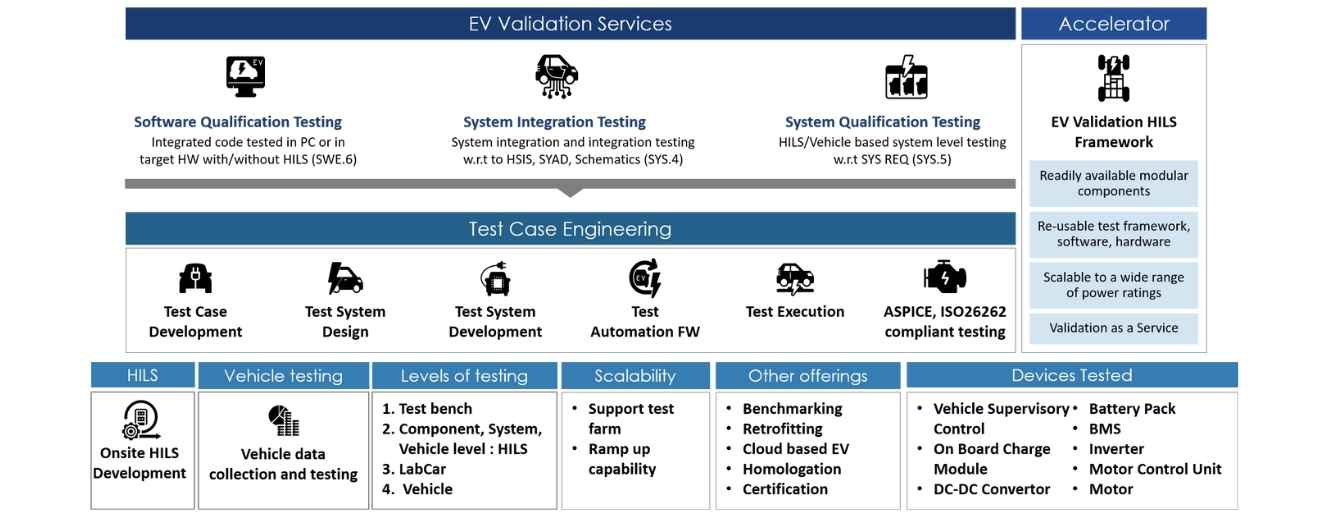
Envision a multi-layered test architecture that combines vehicle-level HILS, NI test benches, and Dyno load simulations. Each layer seamlessly integrates with software & hardware modules to replicate real-world conditions, enabling iterative test cycles for component, system, and vehicle-level validation. The result: a scalable, efficient framework designed for safety, quality, and faster time-to-market.
Whole-Vehicle Validation
Leverage a comprehensive approach to EV testing, ensuring every functional component—from battery systems to powertrain software—exceeds industry standards. By combining hardware simulations and software-driven testing, you achieve robust coverage across vehicle subsystems, guaranteeing safe operation and regulatory compliance in an evolving electrification landscape.
Modular Test Components
Adopt preconfigured, modular components that seamlessly plug into your existing vehicle E/E systems. This approach accelerates deployment, reduces integration complexity, and promotes flexibility for evolving software updates. With high reusability, these components support faster transition from component-level to system-level validation and minimize development overhead for new EV platforms.
Real-Time Simulation & Automation
Drive efficiency through 70% automated, real-time testing. Advanced simulation tools model vehicle dynamics, enabling engineers to recreate driving scenarios without costly on-road tests. This data-driven environment verifies software performance under diverse operating conditions, significantly shortening development cycles while maintaining the highest levels of safety and reliability.
Why Tata Elxsi?
- Proven domain expertise in EV testing and hardware-in-the-loop simulations for complex systems.
- Accelerated time-to-market through prebuilt test frameworks and comprehensive validation solutions.
- Collaboration-ready ecosystem that merges software innovation with global automotive standards.
- Flexible service models tailored for component, system, or vehicle-level testing needs.
- Robust quality compliance powered by functional safety and regulatory best practices.
Information Hub
-
What are the main regulatory challenges faced by EV manufacturers today?
Today’s EV manufacturers must navigate stringent emissions mandates, evolving safety regulations, and standards on battery performance and range. These requirements often vary across regions, making compliance more complex. Coupled with the rapid pace of technological innovation, continuous testing is essential to ensure that all software and hardware components meet or exceed the latest legal and safety benchmarks.
-
How does Hardware-in-the-Loop Simulation (HILS) benefit electric vehicle testing?
HILS replicates real-world operating conditions within a controlled environment, allowing engineers to test how ECUs and software behave under various conditions, such as changes in battery load or driving scenarios. This leads to more accurate data, reduced physical prototyping costs, faster iterations, and ensures safer, more reliable vehicle performance before on-road testing.
-
How can flexible, modular test setups support fast-moving automotive innovations?
Modular test components can be quickly rearranged or replaced to accommodate new software features, ECU updates, or hardware revisions. This adaptability ensures that testing keeps pace with product evolution, minimizing disruption. It also supports scalability, reducing repetitive engineering work and allowing OEMs to capitalize on rapidly emerging EV technologies.
-
Why is functional safety so critical for electric vehicles?
EVs rely heavily on embedded software and intelligent control systems. Any malfunction can have severe safety implications for passengers, pedestrians, and infrastructure. Functional safety standards, such as ISO 26262, help mitigate risks by stipulating rigorous design and verification processes, ensuring vehicle operations remain safe even under fault conditions or component failures.
-
Is real-time testing necessary for every EV system or component?
While not every component demands continuous real-time validation, key systems that govern powertrain function, battery management, or driver assistance often require it. By simulating dynamic scenarios, manufacturers gain insights into software resilience and hardware performance under stress. This approach bolsters reliability, cuts development cycles, and ultimately enhances customer satisfaction.