Case Study
Gen AI-Based Monitoring for Construction and Mining Equipment
Real-time vision analytics for detecting failures, reducing unplanned maintenance, and maximizing fleet productivity.
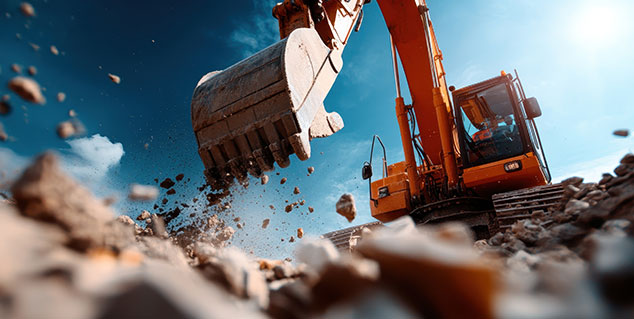
90%
Accuracy in detecting damages
60%
Reduction in unplanned maintenance
3x
Faster failure identification
Background
The customer identified that critical machinery components endure intense wear and impact during earthmoving and mining tasks, and their unexpected failure poses serious safety risks, leads to unplanned downtime, and incurs high repair costs. Currently, inspections are manual, infrequent, and reactive, often delaying the detection of wear or damage.
To address these issues, they are seeking to implement a real-time, automated equipment monitoring system—leveraging sensors, data analytics and predictive maintenance—to transition from reactive to proactive upkeep. This solution aims to enhance operational efficiency, minimize downtime, improve safety, and provide data-driven oversight in challenging mining and construction environments.
Challenge
The customer struggled with the absence of a dependable, automated system capable of real-time detection of missing or damaged equipment components in a rugged mining environment—characterized by dust, heavy vibration, and rough terrain, which complicate accurate monitoring. They needed a scalable solution compatible with different machinery types, deployable without major hardware upgrades, to shift from manual, reactive inspections to predictive maintenance. Their objective was to prevent costly, unplanned equipment failures, reduce labor dependency, and boost operational effectiveness through proactive issue detection in harsh field conditions.
Solution
Tata Elxsi introduced an innovative, AI-driven vision-based equipment monitoring system that uses high-resolution cameras and custom-trained deep learning models deployed at the edge. The solution continuously captures visual data of critical machinery, analyzes it in real time to identify component wear or anomalies, and sends automated alerts to operators and maintenance teams via an integrated dashboard and telematics platform.
By combining synthetic and real-world training datasets, the system is robust across varying lighting, materials, camera angles, and operating conditions. Its lightweight edge AI architecture ensures fast, reliable performance—even with limited connectivity—making it an engaging, scalable upgrade for proactive equipment oversight.
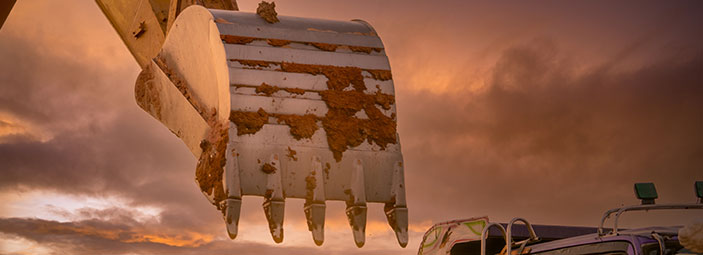
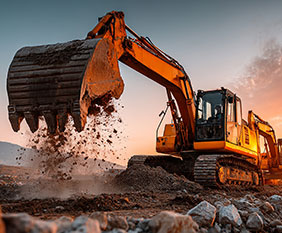
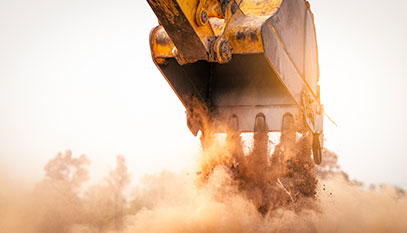
Impact
The deployed vision-based monitoring platform demonstrated impressive results, delivering:
- High accuracy in anomaly detection, achieving better than 95% reliable alerts under varied field conditions.
- Substantial reduction in unplanned maintenance, with incidents dropping by around 30–50%.
- Improved equipment availability, with uptime increasing by approximately 20–30%.
- Lower field repair costs through early intervention was consistent with reported 30%+ maintenance cost savings.
- Rapid, scalable implementation across different machinery models due to its modular AI architecture and lightweight edge deployment - minimizing hardware changes and enabling easy roll-out.
Services rendered
- AI Model Design & Training
- Simulation & Validation
- Agile Development
- Hardware-Agnostic Integration
- Cross-Functional Enablement
- Maintenance Support & Scale-Up