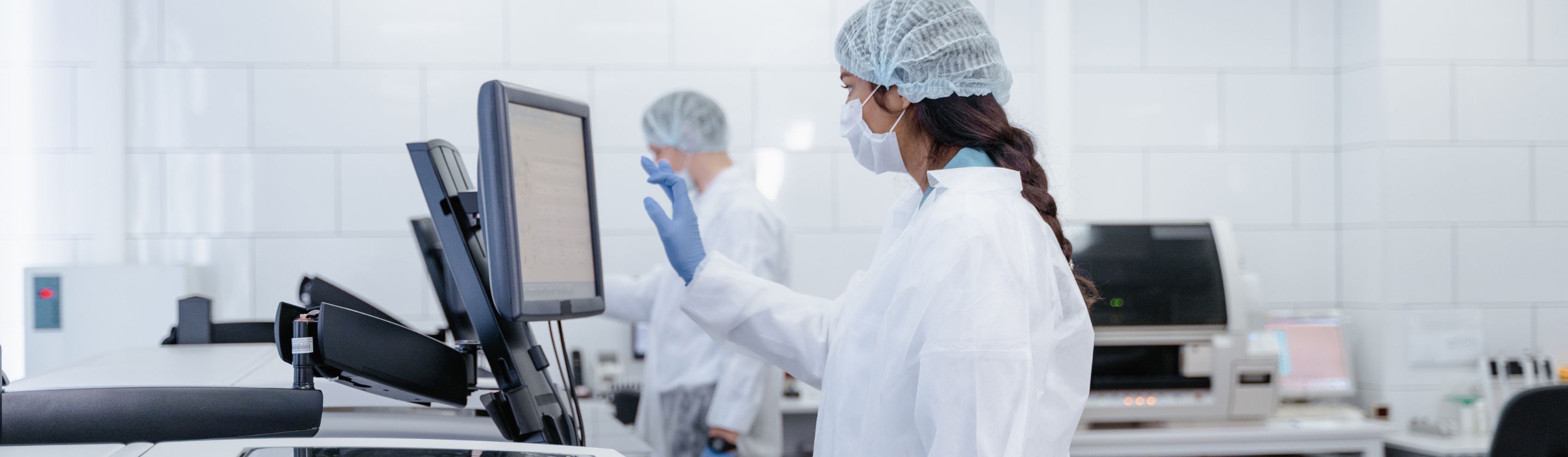
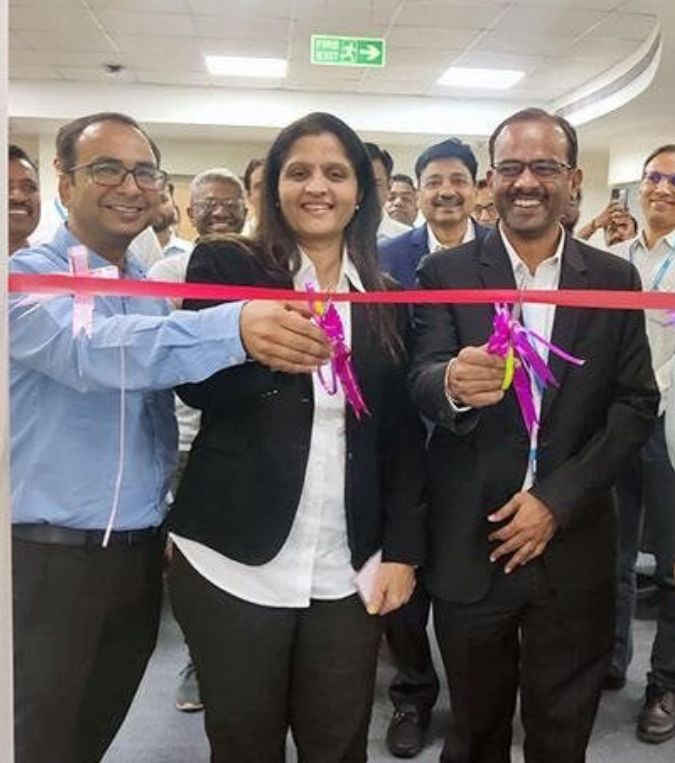
Driving Critical Care Innovation with Dräger
Tata Elxsi and Dräger Establish an Innovative Partnership to Drive Critical Care Innovation in India
Read ArticleQuality and Reliability Enhancements across the Product Lifecycle
Value Analysis & Value Engineering (VAVE) emerges as a strategic method for medical device manufacturers seeking to bolster product performance while optimizing costs. As market competition escalates, organizations leverage VAVE to achieve differentiation, improve clinical outcomes, and expand into emerging markets like China, India, and Brazil. By aligning product features with regional needs, they address price sensitivity and regulatory complexities.
Implementing VAVE ensures robust quality and reliability enhancements across the product lifecycle. From concept to deployment, manufacturers gain a holistic framework that combines cost-down strategies with innovative design, ultimately leading to improved patient outcomes and sustained return on investment (ROI).
A Portable Diagnostic Platform Offering Affordable and Accessible Care
Business Opportunities
Identification of usage gaps, understanding of constraints in emerging markets, ROI, and risks associated with new technology integration must drive the value engineering decisions. Manufacturers must customize products according to the needs of different markets/segments while ensuring benchmarked product quality and performance. Moreover, keeping track of the ROI by analyzing the possibilities and efforts required to carry-out PDLC is crucial. Companies aiming to improve product functionalities with new technology integration must weigh in potential risks and impact on the intended use of the device.
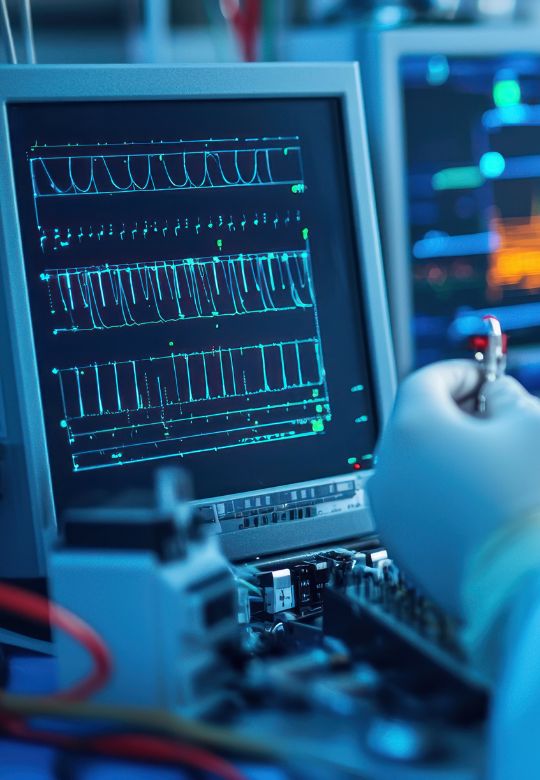
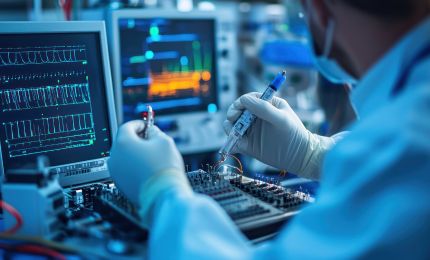
Here’s How We Help
Comprehensive Product Assessment
- Conduct thorough usage gap analyses and stakeholder interviews, aligning solutions with real-world evidence (RWE) and market demands.
- Identify potential risks early through cross-functional reviews, enabling proactive mitigation for improved product quality and reliability.
Tailored Cost-Down Strategies
- Implement multi-level cost reduction methods, including teardown analysis, value benchmarking, and function-cost worth mapping for strategic differentiation.
- Integrate design-to-value principles with robust engineering to minimize resource utilization and maximize product performance for better ROI.
Future-Ready Tech Integration
- Enable connectivity enhancements, IoT integration, and data-driven insights that empower advanced diagnostics and remote monitoring.
- Leverage emerging technologies to upgrade product functionalities, ensuring seamless scalability and a lasting competitive advantage in dynamic markets.
Solution Framework
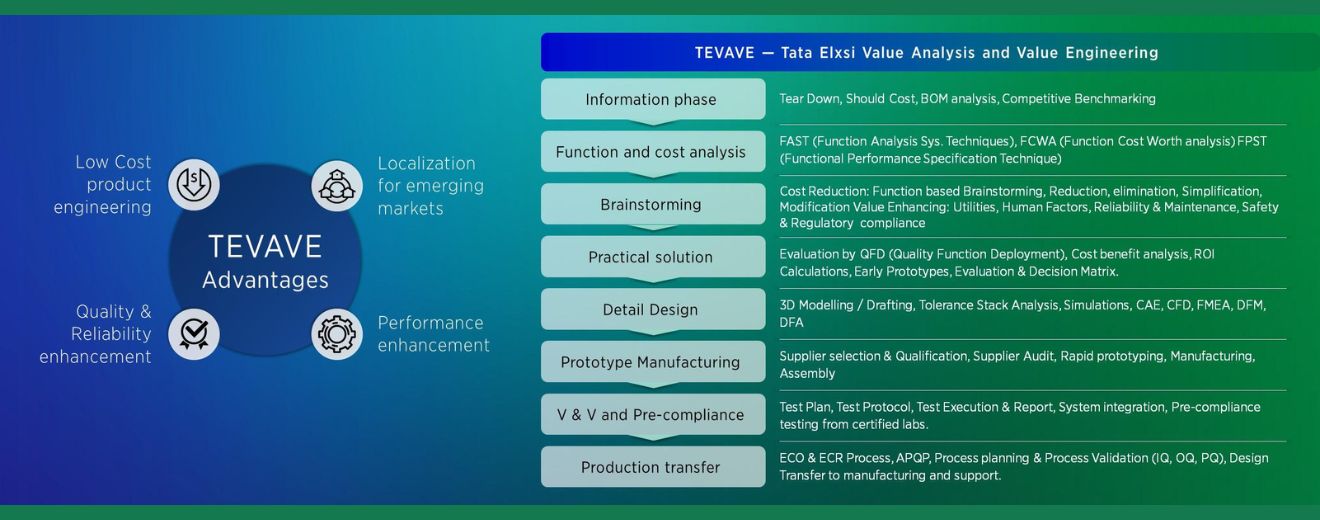
The TEVAVE framework (Tata Elxsi Value Analysis and Value Engineering) is a structured methodology to improve product value by reducing BOM cost, enhancing performance, and ensuring regulatory compliance. It spans the complete lifecycle from teardown and cost benchmarking to design, prototyping, and production transfer. With a strong focus on localization, quality, and manufacturability, TEVAVE enables low-cost, high-reliability product engineering tailored for global and emerging markets while delivering measurable improvements in performance, usability, and regulatory alignment.
Foundational Phases
The journey begins with the information phase, involving teardown, BOM analysis, and competitive benchmarking. Next is function and cost analysis, using techniques like FAST, FCWA, and FPST to evaluate product function against cost. The brainstorming stage focuses on creative reduction, simplification, and compliance-driven ideas to improve utility, safety, and human factors while aligning with regulatory goals.
Solution Development
During practical solution development, tools like QFD (Quality Function Deployment), cost-benefit analysis, ROI calculations, and decision matrices are used to filter and finalize ideas. The detail design phase includes CAD modeling, tolerance checks, simulations, CAE, CFD, FMEA, and DFM/DFA for manufacturability and safety. This is followed by prototype manufacturing, which covers supplier qualification, rapid prototyping, audits, and pilot production.
Testing and Production Transfer
In V&V and pre-compliance, detailed test planning, system integration, and validation with certified labs ensure design readiness. Finally, production transfer enables seamless hand-off via ECO/ECR processes, APQP, and manufacturing validation (IQ, OQ, PQ). Support is extended through robust process planning and post-transfer assistance, ensuring quality, efficiency, and compliance throughout the product lifecycle.
Why Tata Elxsi?
- Decades of cross-industry expertise ensuring informed, insightful, and strategic decisions across complex medical device projects.
- Comprehensive in-house prototyping, testing, and validation capabilities for significantly faster, overall cost-effective product development cycles.
- Robust ecosystem of certified suppliers, accredited compliance labs, and domain specialists for complete lifecycle support.
- Proven multi-level value engineering methodology that optimizes designs, minimizes waste, and ensures long-term product reliability.
- Strong focus on patient-centric innovations driving superior clinical outcomes and remarkable tangible market advantages worldwide.
Information Hub
-
What is Value Analysis & Value Engineering, and how does it benefit my medical device development?
Value Analysis & Value Engineering (VAVE) is a systematic approach to optimize product value by balancing functionality, cost, and performance. In medical device development, VAVE identifies and eliminates non-essential components or processes, ensuring each design element contributes to clinical efficacy and cost-effectiveness. This methodology not only reduces expenses but also enhances quality, reliability, and patient outcomes. By tailoring solutions for emerging markets and established regions alike, VAVE can significantly boost ROI, accelerate time to market, and strengthen competitive differentiation.
-
How does VAVE support product localization for emerging markets?
VAVE involves redesigning products to meet local regulations, cultural preferences, and specific clinical or user requirements. For instance, medical devices targeting China, India, or Brazil might require component substitutions, power specification changes, or modifications in user interface languages. By leveraging comprehensive cost analysis and functional optimization, VAVE ensures that adaptations do not compromise product performance or quality. This localized approach helps brands penetrate new markets effectively, delivering affordable solutions while maintaining global standards of reliability and compliance.
-
Can VAVE help in integrating new technologies like IoT or AI into existing devices?
Yes. VAVE principles extend beyond cost reduction to optimize design for advanced functionalities, including IoT and AI. By prioritizing essential features, analyzing component feasibility, and assessing regulatory implications, manufacturers can seamlessly introduce connectivity and smart capabilities. This not only boosts patient outcomes but also improves real-time data monitoring and predictive maintenance. Through iterative prototyping and cross-functional collaboration, VAVE-based integration lowers risks, shortens development cycles, and ensures that new technologies align with both clinical and market needs for sustainable product success.
-
Is VAVE only about cost reduction, or can it also enhance product reliability and performance?
While cost reduction is a core aspect, VAVE equally focuses on elevating quality and performance. The methodology scrutinizes each functional element to maximize its contribution to overall product value. If a redesign enhances reliability or improves clinical outcomes, it is included even if it adds costs in one area—provided the net value remains positive. By balancing strategic trade-offs, VAVE ensures that product improvements, whether through novel materials or advanced features, do not compromise financial goals but instead strengthen market positioning.
-
How do we measure the ROI of a VAVE initiative?
Measuring ROI in VAVE involves tracking cost savings, product improvements, and revenue gains derived from enhanced performance and market reach. Key metrics include reduced time-to-market, lowered manufacturing expenses, and increased sales in targeted emerging markets. Additionally, improvements in patient outcomes or user satisfaction can lead to higher brand loyalty and repeat business. By comparing baseline performance against post-VAVE results, organizations can quantify both financial and qualitative impacts. Continuous monitoring ensures that return on investment aligns with strategic goals for growth.
-
Why is sustenance engineering critical for medical devices?
Sustenance engineering ensures that legacy and in-market medical devices remain compliant, secure, and supportable. It enables effective obsolescence management, value engineering, and faster adaptation to regulatory changes, extending product life and reducing total cost of ownership. As post-market requirements grow, a strong sustenance strategy is essential.